Did you know that takt planning can shorten a construction timeline by up to 30%, according to leading construction companies Skanska and Fira? But to achieve a large time savings you need to know what is happening on site. This is made possible by sensors.
What does takt time mean in construction?
Takt time is a fundamental concept in lean manufacturing. The goal of lean production is to improve work efficiency by eliminating wasted time, such as unnecessary waiting, overproduction and errors. Followers of Lean principles seek to maximise value and improve competitiveness. Let’s dive into the terminology used in takt time production:
Takt. In takt time scheduling, work phases are divided into chunks of equal length. One chunk is called a takt. A takt is therefore a unit of time. In construction, it’s typically one day or one week.
Takt time. A concept from lean production that describes the time required to complete a single task in a flow-based production process.
The flow principle. The units of the takt plan are scheduled to follow each other in a “flow.” The flow of tasks is created by planning each task according to the length of the slowest task. Each task is scheduled to start as soon as the previous one is finished.
Production train and takt wagon. In takt time production, well-planned work phases proceed in a ‘production train’, similar to the conveyor belt in a factory. The difference is that in construction, the work moves through the product while in a factory, the product moves through the work stages. The work stages follow one another like train cars. Each so-called “wagon”, at any given moment, is parked in its own takt area, which it needs to finish in the assigned time. Takt wagons can also be called work packages.
Takt plan. The takt plan is the visual and strategic plan used to implement takt production. The aim of takt planning is to find repetition in the work phases, so the workload can be distributed correctly. Weekly schedules are planned on the basis of the overall construction project timetable. Regular weekly meetings are held to check whether the previous week’s timetable was implemented as planned. The timetable is updated based on what has been learned.
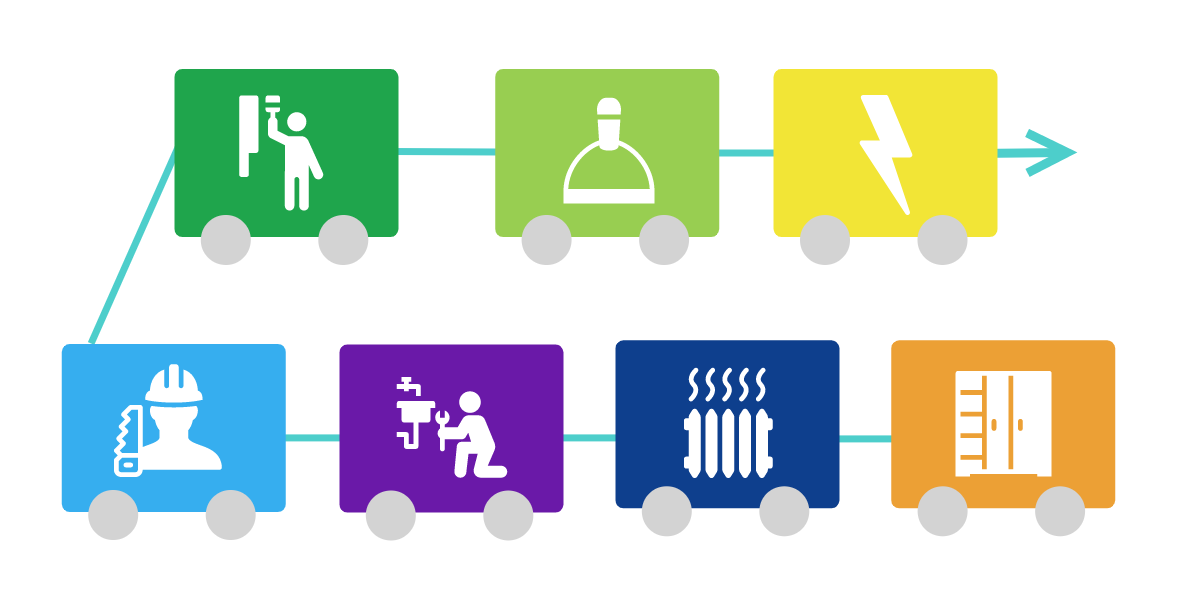
What are the benefits of takt time production?
Takt time production works best in construction projects where there is a high degree of repetition. These can include apartment building renovations, interior finishing work on apartment blocks, and plumbing renovations.
There are many benefits to be gained from takt planning in construction. A steady flow makes the project more predictable, reduces the lead time, and lowers costs. Useful for all parties involved!
Takt planning enables the materials and other resources required on a construction site to be available at the right time. Each person involved knows what to do, when, and where. The next phase of work on the site starts as soon as possible after the previous one has finished.
The purpose of time-based production is not to increase the rush and speed up the completion of tasks, but to increase the time available for completing tasks and make production more efficient in a rational way. By following a carefully planned timetable, you have more time to get the job done. Optimally takt time production results in more getting done with less work. An ideal situation!
Why is implementing takt planning demanding?
Creating a flow schedule, breaking it down into appropriate work phases and sticking to it can be challenging. Takt time production in construction requires close cooperation between the general contractor, subcontractors and suppliers, good advance planning, and early commitment from subcontractors to meet the schedule.
Because the takt schedule determines when each work phase starts, the main contractor must have all workers, materials, and equipment rentals on site at the time they are needed. For many subcontractors, this is a new and different way of operating. They may be used to deciding themselves which site they’ll go to on which day.
Takt time production works best in design-build contracts, where the main contractor has more control over the project’s schedule and progress.
How do sensors help in takt time production?
To create a more efficient site and speed up the schedule, site managers need to know what’s happening on site at all times. However, site management tools (e.g. Fieldwire, Procore and Autodesk Construction Cloud) don’t usually include ongoing measurement data. It’s not possible to know where the different equipment is located on site, or if half the apartments on the third floor are colder than they should be.
Such data can only be collected by IOT sensors, small devices connected to the internet. Data can be collected on temperature, humidity, acceleration (impacts), and the location of equipment and workers, among other things.
Sensors can help stay on schedule in the following ways:
- Locating workers
Worker positioning is critical for staying on schedule. Because the schedule is planned well in advance, it’s important to be able to see how much time specific tasks actually take in practice. Analysing location data can uncover obstacles that are slowing work down, like waiting, searching for tools, or tasks performed in the wrong order. Project schedules can also be better planned in the future. Kaltiot offers a GDPR-compliant solution for employee tracking.
- Monitoring ambient conditions
By monitoring site conditions, such as temperature and humidity, construction work can continue according to schedule. Interior work can be started more quickly when conditions are kept at the optimal level for structures like concrete slabs to dry.
When the structure dries according to schedule, work is able to proceed smoothly.
Damp structures are one of the biggest challenges to construction schedules. When it’s discovered that the floor slab in some apartment isn’t dry and you have to wait a several weeks longer, that apartment will probably fall behind schedule for the entire rest of the project.
When random apartments fall behind schedule, the it becomes significantly more difficult to manage the entire project. Workers are forced to return to previous floors to complete the delayed work out of order. Construction site logistics become more complicated when drywall, flooring, and cabinets are needed in different places at different times, rather than in the logical order that was in the original plan.
Delays also mean new negotiations with contractors. The main contractor will have to agree on new schedules with installers, who may already have other work scheduled at different sites. Delays can also mean bottlenecks within a project. Workers alternately have too little and too much to do, because the number of work stations reaching a certain stage varies from week to week.
- Monitor the location and use of equipment
Time spent looking for equipment is time wasted, creating uncertainty in the schedule. Construction schedules don’t have room for non-productive work. Sensors help you to quickly locate equipment for shared use on site, such as scissor lifts, personnel lifts, mobile workbenches and heaters. Employees can easily find devices by looking up the location of the device in the app on their smartphones.
- Locating material deliveries
A lot of time is also spent searching for materials on site. Sensors can be used to track the arrival of materials on site and see where they are located. This allows workers to get to work, without the delays caused by lost materials on a tight schedule.
Kaltiot’s sensors make takt time production easier.
Kaltiot Smart Tracker gives site management, the client and contractors a clear picture of what is happening on site: what is where, how the drying process is progressing, whether painting or parquet installation is ready, and how much time different workers are taking to complete a task. More accurate schedule estimates mean that time can be used more efficiently on the construction site and the overall project schedule can be accelerated without rushing.

The Kaltiot Smart Tracker has many benefits on a construction site:
- Small and discreet size: the compact size makes it easy to place the sensor where it is not in the way of work
- Portability: easy to move from one room to another as the work progresses
- Longevity: the sensors are durable and long-lasting – only the batteries need to be replaced from time to time
- Low power: BLE technology consumes little electricity – experience shows that battery life is at least sufficient for on-site use
Interested?
Read more about our services on construction sites.
Sources used in the article:
Heikkinen, Simo-Veikko. Timetable for the internal completion of the construction phase. Thesis. RETRIEVED 2019. https://www. theseus.fi/bitstream/handle/10024/264785/Heikkinen_Simo-Veikko.pdf?sequence=2
Easton, Spencer & Schroeder, Jason. What is a Takt plan? Lean Construction Blog. 3.1.2022. https://leanconstructionblog.com/What-is-a-Takt-plan.html