Stock photo.
Kaltiot and Sapotech developed a monitoring solution together which was used to gain more visibility into a Scandinavian steel plant’s processes. Sapotech is a Finnish company which produces innovative high technology products and systems for monitoring quality and processes in the metal and steel industries.
The steel plant needed an automated solution to track steel ladles
The factory in which the solution was taken into use produces high-quality stainless steel from scrap metal. The factory is a leader in the recycling economy and sustainable development in the steel industry. It’s also one of Europe’s largest material recycling plants.
The factory has about 40 steel ladles, which are used to transport molten steel at temperatures of about 1600C. A steel ladle is a large, bucket-shaped container which is lined with fireproof materials. When full, a steel ladle can hold as much as 100 tons of molten steel.
During the steel production process, the ladles are moved around the melt shop from one place to another. The high temperature of molten steel wears away at the fireproof lining, and so the ladles also require maintenance from time to time.
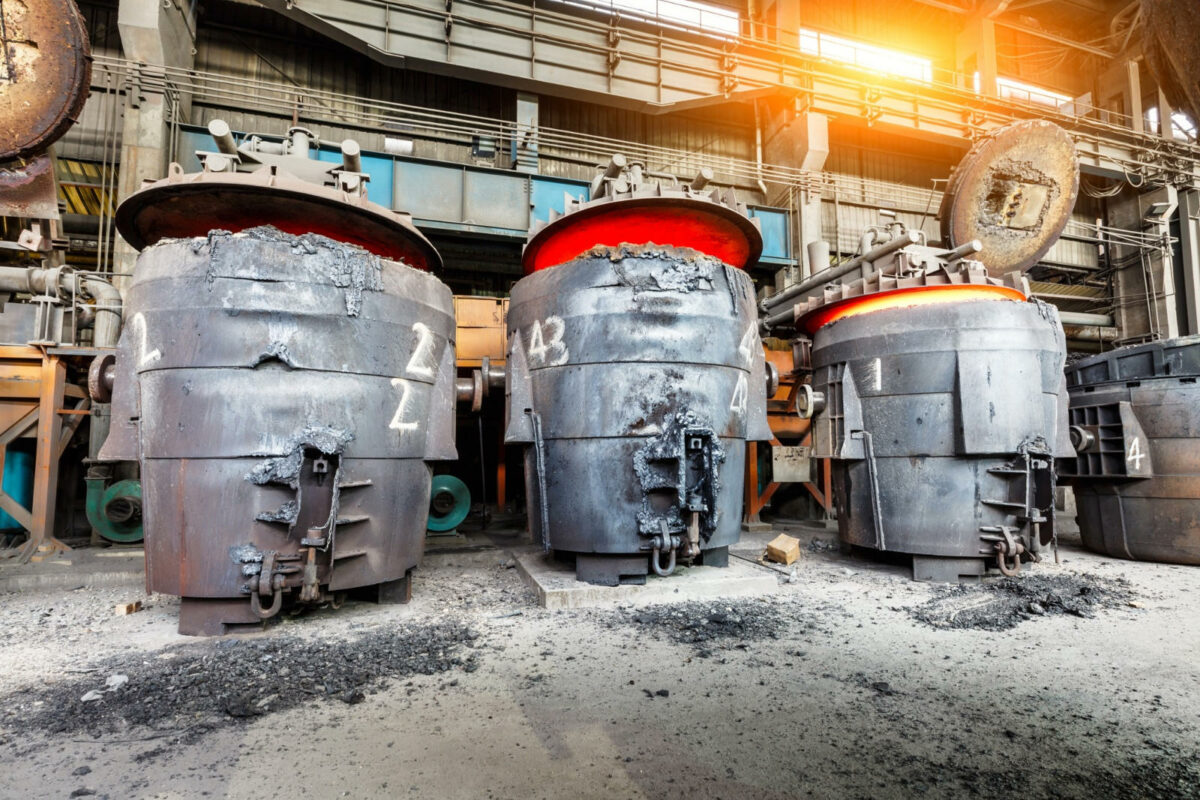
Why track ladles?
There were many reasons to track steel ladles, such as:
- Scheduling is easier when employee know how many ladles are in use and where they are.
- A ladle that is already hot can be used again without needing preheating. This reduces energy usage.
- Historical location information helps to optimize maintenance intervals, which lengthens the lifespan of the ladle’s lining and thus reduces expenses.
What does the tracking solution consist of?
The solution developed by Kaltiot and Sapotech automates tracking of the ladles and reduces manual work as well as improving the quality of data. The solution consists of the following components:
- A tracking sensor in a heatproof container
- An indoor tracking network, which consists of small BLE beacons which enable accurate tracking of the tracking sensor
- Gateways which send the location information to the Kaltiot cloud
- Kaltiot Smart Tracker service and reporting
- Forwarding of the location data to the steel company
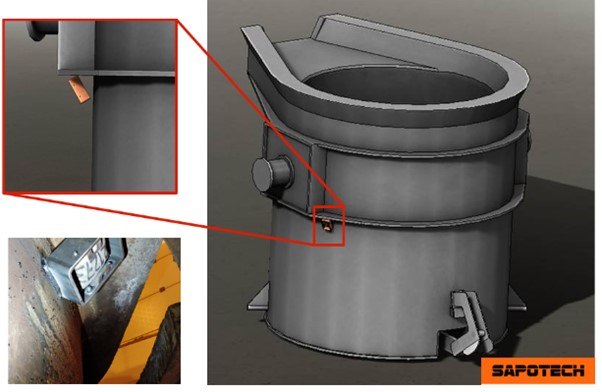
An example of how the tracking sensor can be attached to a steel ladle
Combining heat and electronics
The special conditions of a steel plant brought their own challenges to the project. The temperatures next to a steel ladle can reach several hundred degrees Celsius. Any sensor attached to a steel ladle needed to be able to withstand severe heat and splashes of molten metal.
A special protective case was built to protect the sensor and its battery from melting.
This protective case, as well as the steel ladles themselves, which block radio transmission, made it challenging to get the sensor’s wireless connectivity to work. A working solution was found by testing various protective case designs and attachment points in real-life conditions.
Kaltiot’s and Sapotech’s joint project began in March 2020. The finished solution was launched at the steel plant in 2021, after the product development and pilot phases.
Benefits of the solution
A new technology always needs to bring more benefit than it does additional work. That’s why we always focus on bringing our customers a down-to-earth and functional solution. In this IoT project, the main benefits were fast installation, the ability to install tracking without needing to make changes to existing equipment or infrastructure, cost effectiveness, and the opportunity to combine the newly generated location data with other reporting.
The fourth industrial revolution
The environmentally friendly digital solution is part of the 4th Industrial Revolution, that is, the digitalization and automation of industry.
Sapotech’s Chief Metallurgist, Juha Roininen, says it’s important that there are innovative steel plants in Finland and Scandinavian countries that are working to make the metal industry more energy efficient and environmentally friendly.
“With the developed solution, we can create clear cost savings for the customer, and there is no doubt that the customer will get value for their investment. When we talk about energy- and material-intensive industries, affordability guarantees a quick payback period for the investment,” comments Juha Roininen.
An innovative culture is very important for the future of the steel and metal industry.
Looking forward
In the future, the goal is to integrate the tracking solution more deeply in order to optimise the melt shop processes even further.
Juha Roininen commented on the cooperation with Kaltiot as follows:
“Kaltiot is a very active player. They understand that industrial development processes require perseverance and patience, and they have both. Kaltiot considers the ecosystem between different parties important. It’s also important to cooperate with academia, where the benefits of this solution are taken forward through modelling. Further development to utilise the data is carried out, for example, in our joint project with this steel company.”
The ladle monitoring system was developed in the AMET project funded by Business Finland and led by Sapotech. The aim of the AMET project is to improve the efficiency of steel manufacturing processes and reduce environmental impact. The project develops industrial-scale process monitoring systems and expert systems for selected steel manufacturing processes, such as electric arc furnaces, continuous casting and rolling. The project will develop an operating model based on the platform economy, which will enable metal refiners to benefit from the cost-efficiency and rapid product development of SMEs.