Finnish construction company Fira keeps moisture management in residential buildings in balance with remote monitoring from Kaltiot. Fira can see where on the construction site action is needed to get the temperature and moisture balance right. Fira’s systematic management of conditions ensures that the workflow remains optimal and construction phases progress according to schedule.
The first on-site pilot of the Kaltiot IoT solution started in 2018. We covered it in our blog post “Smart Tracker in use on a construction site.”
Continuous and comprehensive measurement for moisture management
It’s impossible to maintain the temperature and humidity balance of a building during the frame and interior construction phase without ongoing, comprehensive measurement. A construction site is not a factory, where work takes place in precisely controlled conditions. It’s a harsh and constantly changing environment.
From a drying perspective, the different seasons alone place completely different demands on both the equipment and the process, resulting in three different approaches to controlled drying. Counter-intuitively, summer (in Finland) is the most difficult, winter is the best and the intermediate season something in between, depending on how much rain falls and how often.

Remote monitoring of temperature and humidity can help to identify where in the building measures are needed to remove moisture or control heat. The data can also be used to measure whether enough dry air is being produced, whether the building is warm enough, and whether a wet space is being ventilated effectively enough.
A construction site is not like a factory, but the work points on a site flow through the product being built. Improving the working conditions at the workstations is challenging because the workstations keep moving forward as the previous one is completed. For this reason, IoT devices need to be multifunctional and cost-effective from an investment perspective. Although the construction time is seemingly long, the interior phase on a takt time site lasts only a few weeks. The sensor platform solution must allow for quick and easy deployment, maintainability and migration to the next site at minimum cost. Kaltiot Smart Trackers are ideally suited to these needs,” says Fira’s Development Director Otto Alhava.
How Fira uses Kaltiot Smart Tracker to monitor conditions
Collecting data
In practice, one device for measuring humidity, temperature and pressure is installed in each apartment.
These sensors, which use wireless technology, are installed in a location that will stay out of the way of work in the interior phase while obtaining the most accurate measurement possible.
The sensors send the condition data to the Kaltiot cloud service via a gateway device. The data is further transferred to Fira’s own platform, from which Fira creates a situational picture of the conditions for each construction site as part of the site’s overall project management dashboard. The cloud-based system allows results to be monitored and analysed anywhere, anytime. Data flows into the system from the site without interruption, keeping monitoring in real time.
Using data for decision-making
The measurement data will show any work that increases the moisture or cold load, such as material deliveries, tiling, levelling, and painting. The ongoing monitoring also provides an overall picture of the thermal and moisture balance of the building as work phases progress, which in turn can be used to develop more efficient drying models.
Fira uses Kaltiot Smart Tracker to manage conditions throughout the entire construction project. Kaltiot’s solution has provided the following benefits to Fira’s housing construction:
- Data generation and collection: Fira has been collecting comprehensive data on the conditions of its sites for more than four years and has collaborated with Aalto University to develop a drying model for residential apartment buildings.
- When the drying model works, the building dries on target and work progresses on schedule.
- Smoother workflow
- Reduced lead time
- High efficiency
- Reduced carbon footprint
- Better understanding of humidity and temperature conditions
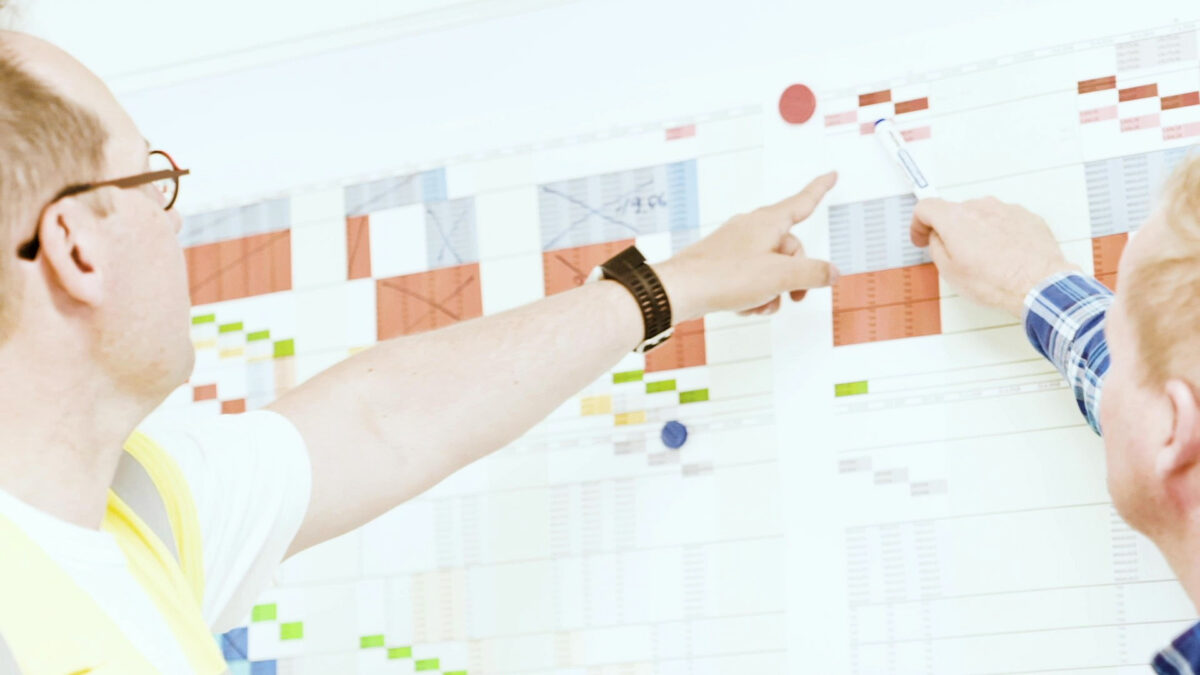
Monitoring enables cost- and energy-efficient construction
Dehumidifying a site requires the production of a large amount of heated and dry air. Producing warm, dry air, on the other hand, requires a lot of equipment and resources, which takes up electricity and other energy, as well as workers’ time. So it’s essential to send that heat to exactly where it’s needed in the building, so all this work is not wasted.
Reducing the carbon footprint of construction
By site drying with the Smart Tracker, Fira has gained more accurate information about drying efficiency. Drying efficiency is the how much warm, dry air has been produced in relation to how much the structures dry out. Monitoring air conditions has helped to improve drying efficiency.
Overall, the site workflow is smoother, lead times are reduced, and the carbon footprint is reduced when moisture management measures can be precisely targeted to the right location in real time according to real-time needs.